This delicate technique consists of printing the decoration in black on the raw biscuit, then filling each cell thus circled with a coloured enamel.
This manual technique is carried out by an experienced craftsman and it takes several years of training before perfect mastery is achieved.
All the pieces produced by the Faïencerie bear our mark and are accompanied by a Certificate of Origin.
MOLDING
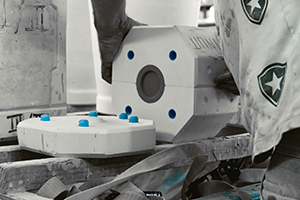
The shape of the piece is created by our stylists and a plaster model is made by our modelling workshop.
MODELLING
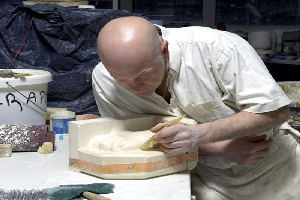
This model generates a hollow plaster mold, into which the slip (a mixture of kaolin, clay and water) is poured. The plaster of the mold, eager for water, sucks the liquid from the slip in contact with its surface: a crust forms along its walls. As soon as the crust is 7/8 mm thick, the mold is turned over, emptying the excess slip still inside.
RACHEVAGE
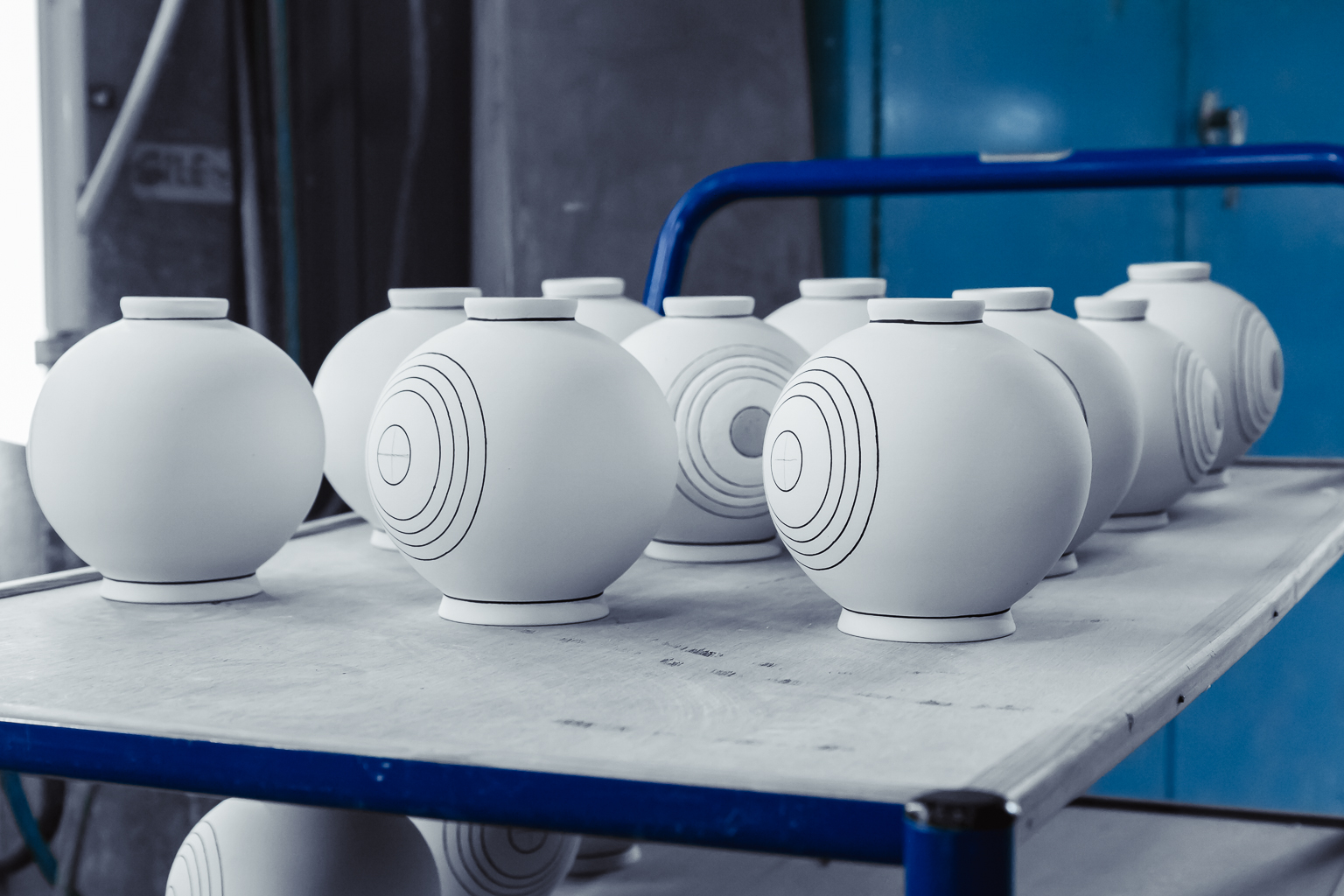
The piece then dries in the mould for 4/5 hours, then is removed from the mould and left to air for 24 hours. The racheveurs deburr the parting lines and give it a smooth appearance by rubbing it with a sponge, before a first firing at 1050° C for one night.
When it comes out of the kiln, this white clay is called biscuit.
BLACK DRAW
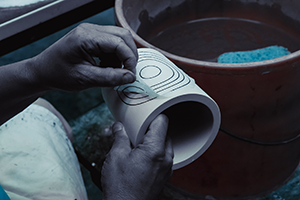
The biscuit is printed with a line of black ink that takes up the decoration to be applied.
DECORATION
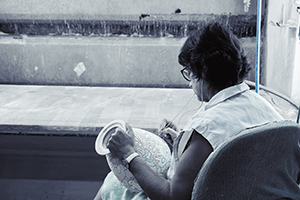
Each cell created by the line is then filled by hand with coloured enamel using a drop-by-drop technique. As the drop of enamel dries almost immediately on contact with the biscuit, it is impossible to 'paint' this piece, hence the use of the technique which consists of placing one drop of enamel next to another until the entire cell is filled with colour.
LAYING OF THE GOLD
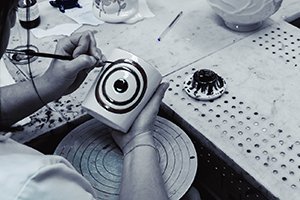
Once the piece is completely enamelled, it is fired at 750°C overnight. A retouching operation then takes place, requiring a second firing at 750°C, then the gold is brushed on before a final firing at 600°C.
SIENNA
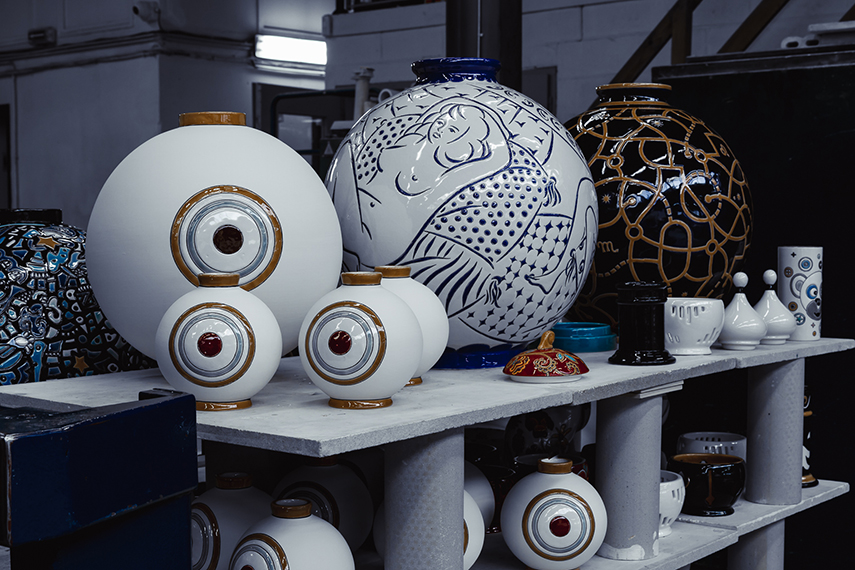
The final operation is to pass sienna over the glazed surface to make the cracks in the glaze visible, and the piece is finally finished.