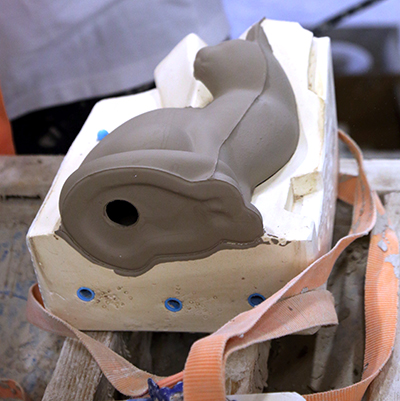
The shape of the piece is created by our stylists.
A plaster model is then made by our modelling workshop. This model, once moulded, generates a hollow plaster mould into which the slip (a mixture of kaolin, clay and water) is poured.
The plaster of the mould, eager for water, sucks the liquid from the slip into contact with its surface: a crust forms along the walls of the mould. Once the crust reaches 7/8 mm in thickness, the mould is turned over, emptying the excess slip still inside.
The piece then dries in the mould for 4/5 hours, then is removed from the mould and left to air dry for 24 hours. The racheveurs trim the parting lines and give the piece a smooth appearance by rubbing it with a sponge. The piece is then fired at 1050°C overnight.
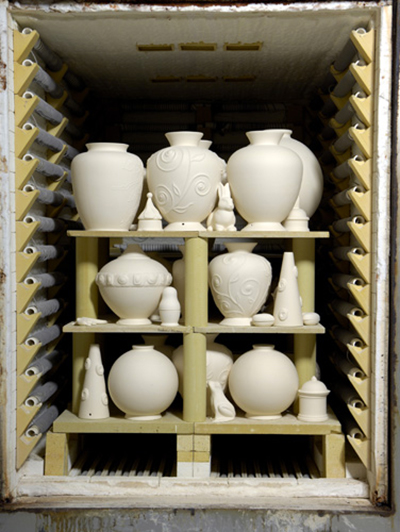
This white clay is called biscuit.
The biscuit is printed with a line of black ink that repeats the decoration of the piece and partitions the colours, preventing them from mixing. Each cell created by the line is then filled by hand with coloured enamel using a drop-by-drop technique.
As the drop of enamel dries almost immediately on contact with the biscuit, it is impossible to "paint" this piece, hence the use of the technique which consists of placing one drop of enamel next to another until the colour cell is completely filled.
One piece is completely filled by the same decorator.
Once the piece is completely enamelled, it is fired at 750°C overnight.
The piece is then retouched, requiring a second firing at 750°C, then gold is brushed onto the decoration and the piece is fired again, this time at 600°C. Sienna is then passed over the enamelled surface to make the cracks in the enamel visible, and the piece is finally finished.
This specific technique, very delicate to implement, requires a particular expertise from our craftsmen.
The result is well worth the effort: the layer of coloured enamel is very thick and produces a volume and depth of colour that is generally impossible to reproduce in decorated earthenware.